Solar PTL follows a long tradition that started with the Photovoltaic Testing Laboratory at Arizona State University (ASU-PTL).
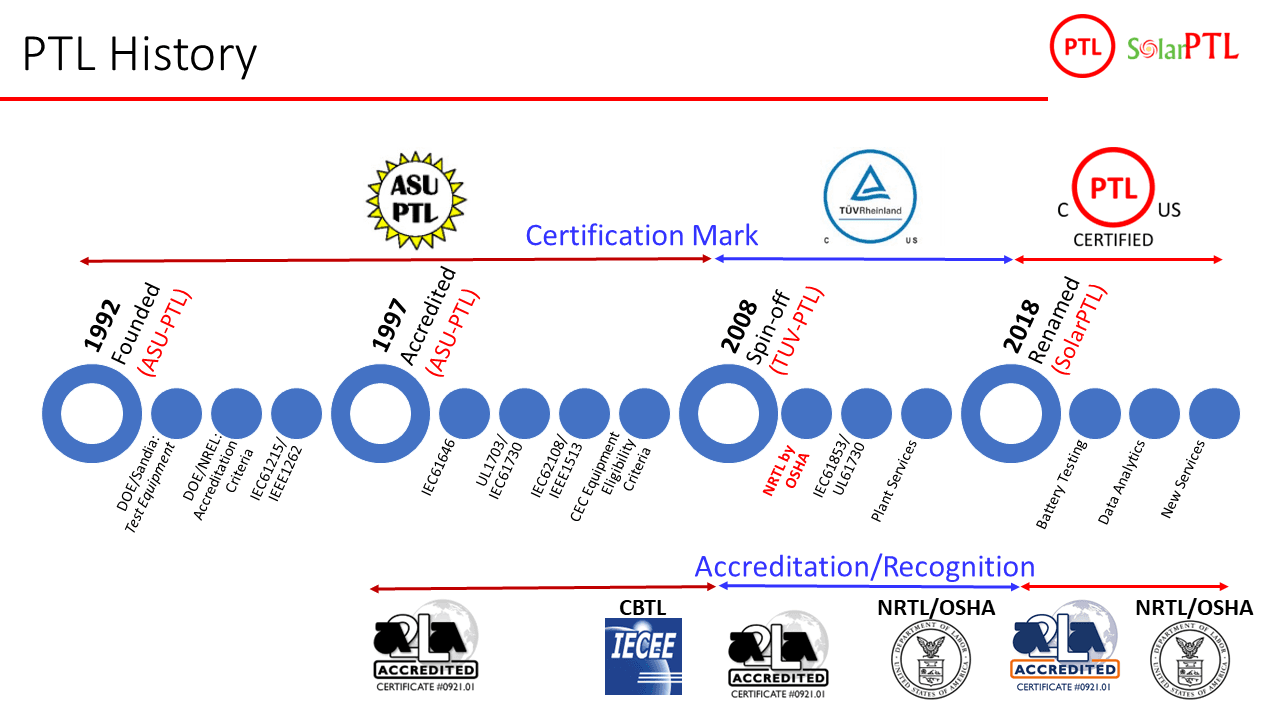
ASU-PTL Birth
October 21, 1991: Letter from Bob Hammond to Dr. Chuck Backus: “…Wouldn’t you like to have an internationally recognized PV module qualification facility located at ASU?”
November 25, 1991: Dr. Backus, Dr. Wood, and Mr. Bob Hammond (Fig. 1) met at Denny’s (fast food restaurant) in Tempe, Arizona; and agreed to establish a “Photovoltaic Testing Laboratory” (PTL) at Arizona State University (ASU) with a start date of January 1, 1992. The objectives were defined as followed:
- Develop a hands-on training laboratory for graduate and undergraduate students;
- Provide state-of-the-art laboratory equipment with which faculty, staff, and students could perform research related to Photovoltaic (PV) module reliability, durability, and performance;
- Establish the capability to perform qualification testing per all relevant national and international standards, including Underwriters Laboratories (UL) 1703;
- Provide PV module qualification testing services to the PV industry;
- Provide related applied research to the PV industry;
- Develop a partnership between ASU and the PV industry;
- Develop a close working relationship with the national laboratories and electric utilities;
Eventually expand the laboratory to include an all PV balance of system components and PV systems (stand-alone and grid-connected PV systems).
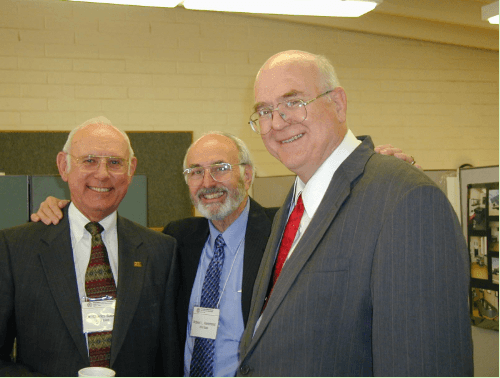
The Center for Energy Systems Research (CESR), an organization within the College of Engineering and Applied Sciences, was the administrative unit which supported the establishment and development of the PTL. The CESR hired Bob Hammond as the program director on January 2, 1992.
On December 9, 1991, Mr. Bob Hammond received an offer letter from the CESR to serve as the program director, the main task being to “…work with the Center to develop a self-sustaining Photovoltaic Performance and Qualification Test Facility”.
ASU-PTL Evolution
Two events occurred in 1992 that established the beginning of the PTL in terms of hardware PTL Evolution:
First, Marjorie Tatro of Sandia National Laboratories (SNL) provided ASU with a contract to develop the “ideal” hail impact tester. The contract included a list of “best effort” specifications and no constraints on the product design. Two undergraduate students, David Gavin and Ryan Sanders, developed a conceptual design and prototype for Mechanical and Aeronautical Engineering (MAE) 490 course credit. With the assistance of the ASU Engineering Lab Services model shop, Mr. Gavin and Mr. Sanders created a prototype that evolved into a product that met all of the SNL requirements for the ideal hail impact tester. A third individual, Nick Gilbert, played a key role in the final stages of design and construction of the tester. At this time, an additional test station was constructed for use at PTL.
Second, Marjorie Tatro provided ASU with a surplus environmental chamber. This chamber, originally used by the Jet Propulsion Laboratory (JPL) for PV module environmental tests, was shipped to ASU in mid 1992 and installed at ASU over the next twelve months. This placed ASU in the unique position of being the only non-government laboratory in the world with a PV module hail impact tester.
Two important events occurred in the summer of 1996: (1) The first multi-client qualification test program was completed in June; (2) and in July the PTL moved to the new ASU’s Polytechnic campus (ASUE) campus in Mesa.(figure 3) The move to the Polytechnic campus provided the space required to fully develop an international testing laboratory. An organizational change also occurred at this time with PTL now reporting to the Electronic and Computer Engineering Technology Department (ECET), a unit of the College of Technology and Innovation (CTAS)
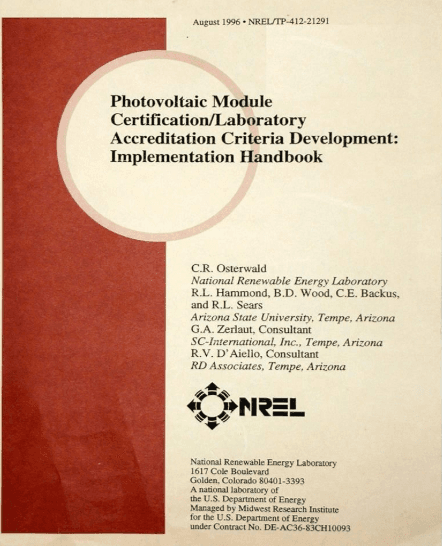
The first multi-client qualification test program
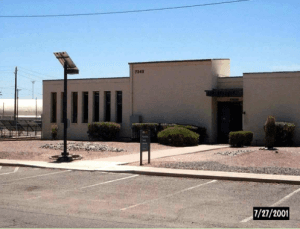
PTL @ new ASU Polytechnic Campus
In August of 1996, an additional environmental chamber, manufactured by Russell’s Technical Products, was installed at the new lab facility. This was just in time to begin the Springborn Testing and Research (STR) contract. STR operated under contract to the National Renewable Energy Laboratory (NREL), which in turn was funded by the Department of Energy (DOE). NREL then subcontracted to ASU to conduct qualification tests and outdoor exposure tests on modules using new formulations of ethylene-vinyl acetate (EVA).
ASU started the IEEE 1262 qualification-testing program for STR in July 1996 and completed these tests in January 1997.
In December 1996, the PTL applied for accreditation to the American Association for Laboratory Accreditation (A2LA). A2LA was chosen for this task because it is one of two agencies within the U.S. recognized to accredit laboratories to the International Organization for Standardization (ISO) Guide 25, General Requirements for the Competence of Calibration and Testing Laboratories. This accreditation would also recognize ASU-PTL’s compliance with the relevant International Standards Organization (ISO) 9000 series of standards as well as PV-1, Criteria for a Model Quality System for Laboratories Engaged in Testing Photovoltaic Modules. The A2LA audit was completed on March 21, 1997. The audit resulted in a total of eleven deficiencies (the majority of which were the result of calibration laboratories that the PTL used) and these deficiencies were corrected by June 3, 1997. Accreditation was awarded on June 23, 1997 and made the PTL one of only three laboratories in the world that were recognized as accredited testing laboratories in the field of photovoltaics. Accreditation is being successfully renewed every two years.
In 2000, a third environmental chamber was installed. This chamber was designed specifically for “Thermal Shock” tests of PV modules. With three chambers online, all three environmental tests (temperature cycling, humidity-freeze, and damp heat) can be conducted in parallel, reducing the total qualification test time from 110 days to 90 days.
In addition to serving the photovoltaic industry with PV module testing services, the laboratory has trained many undergraduate students and graduate students in photovoltaic testing procedures. In September 1998, a classroom was established within the PTL facility. In August 2001, ASU-PTL was qualified by Underwriters Laboratories Inc. (UL) to participate in its Third Party Test Data Program. The program allowed PTL to perform qualified safety testing on photovoltaic modules to the UL 1703 standard. The test results were then reported directly to UL after test performance. This helped the PV manufacturer by providing faster quotation response time from PTL, and full test witnessing by UL was no longer required. The UL Qualification was successfully renewed every year until it became TUV-PTL in 2008 (in October 2008, ASU-PTL became TUV-PTL).
Effectiveness and efficiency of formal classroom training.
As of the fall of 1996, Arizona State University’s third campus, Arizona State University East (ASUE), began operation with degree programs offered in both the College of Technology and the School of Agribusiness and Resource Management. The ASUE campus was created from the acquisition of property from the Williams Air Force Base, located at 6001 South Power Road in Mesa, Arizona. The ASUE philosophy is to offer students a unique learning environment that has been termed an academic village. This village, which encompasses the Williams Campus, is composed of ASUE, Chandler-Gilbert Community College, Emery-Riddle Aeronautical University, Mesa Community College and industry-supporting laboratories such as the U.S. Air Force’s Armstrong Laboratory and the Photovoltaic Testing Laboratory (PTL). This unique learning environment allows students to take courses offered through all local colleges as well as to supplement their learning with experience from contract laboratories.
From ASU-PTL to TUV Rheinland PTL
At around mid-2007, what started with a simple “wouldn’t you like to have an internationally recognized PV module qualification facility located at ASU?” question in 1991 has now become a pioneer in a global emerging community. ASU-PTL had reached some very encouraging milestones:
- Fully-functional, self-sufficient accredited laboratory
- A2LA Accreditation: June 1997
- PMC Accreditation: July 1997
- IEC Q/PVGAP Accreditation: February 1999
- UL 1703 Third Party Test Data Program: August 2001
The ONLY accredited PV laboratory in the US After 10 years of operations, the TUV Rheinland Group decided to turn their “focus to other areas within the Products testing business” in North America. Mr. David Leers, then Regional Manager North America, added: “Considering the existing regulatory and business environment, the solar testing business in the US is no longer part of our core strategy”.
ASU-PTL strengths included:
- An internationally recognized and respected testing lab for its commitment to PV testing excellence!
- A self-supporting laboratory that receives no appropriated funds from ASU, State Government or Federal Government.
- One of only three to five laboratories in the world that performs photovoltaic panel testing.
- The only test lab to provide both Safety & Performance Certifications for businesses in multiple countries.
Test results accepted by the US safety certification bodies, European safety certification bodies and Asian (Japan) certification bodies
The difficult takes time. The impossible takes a little longer - and requires a total commitment to achieving the goal. However...
- The market was growing at 30-40% YOY
- The industry was growing at an annual rate of approximately 50% YOY
- The ASU-PTL was outgrowing its building facilities
- There were extensive delay in investing for additional equipment and expanding the facility to meet the market demand
- Four new testing laboratories were about to open that will compete directly with the ASU-PTL
The Underwriters Laboratories (UL) was planning to build a laboratory in the Silicon Valley As a non-profit organization that was part of an academic institution, ASU-PTL was not equipped to compete. As a result, in November 2008, ASU entered into a joint-venture (JV) with TUV Rheinland North America to form TUV Rheinland PTL. The key commitment of this JV was “the continuation of service and quality of the PTL to the manufacturers”.